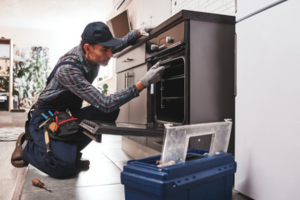
Appliance Repair
Welcome to our comprehensive guide on mastering advanced troubleshooting techniques for appliance repair technicians. In this blog, we’ll delve deep into the technical aspects of appliance repair, equipping you with the knowledge and skills needed to tackle even the most challenging issues with confidence and precision.
Understanding Circuit Analysis and Component Testing
In the dynamic world of appliance repair, mastery of circuit analysis and component testing is essential. From diagnosing electrical faults to pinpointing the source of malfunctions, this foundational skill set forms the bedrock of effective troubleshooting. In this section, we’ll explore the principles of circuit analysis and delve into the intricacies of component testing, providing you with the tools to navigate the complex wiring and electrical systems found in modern appliances.
A. Principles of Circuit Analysis
- Ohm’s Law: At the core of circuit analysis lies Ohm’s Law, which states that the current flowing through a conductor between two points is directly proportional to the voltage across the two points and inversely proportional to the resistance between them. By applying Ohm’s Law, technicians can calculate current, voltage, and resistance within circuits, facilitating diagnosis and troubleshooting.
- Kirchhoff’s Laws: Kirchhoff’s Laws govern the behavior of electrical circuits, providing principles for analyzing voltage and current distributions. Kirchhoff’s Voltage Law (KVL) states that the total voltage around any closed loop in a circuit is equal to the sum of the voltages across each component. Kirchhoff’s Current Law (KCL) dictates that the sum of currents entering a junction in a circuit must equal the sum of currents leaving the junction.
B. Component Testing Techniques
- Multimeter Usage: The multimeter is a versatile tool used to measure voltage, current, and resistance in electrical circuits. By employing the various functions of a multimeter—such as voltage mode, current mode, and resistance mode—technicians can assess the health and integrity of electrical components within appliances.
- Continuity Testing: Continuity testing is employed to determine if there is a continuous electrical path between two points in a circuit. By checking for continuity across switches, fuses, and wires, technicians can identify open or broken circuits that may be causing appliance malfunctions.
- Voltage Drop Testing: Voltage drop testing involves measuring the voltage difference across components or connections in a circuit under load conditions. By comparing voltage readings before and after specific components, technicians can pinpoint areas of high resistance or voltage loss, indicative of faulty connections or components.
- Resistance Testing: Resistance testing is utilized to assess the resistance of electrical components within a circuit. By measuring resistance values using a multimeter, technicians can determine if components such as heating elements, thermistors, or temperature sensors are functioning within acceptable parameters.
Understanding Electronic Control Systems
In the intricate landscape of modern appliances, electronic control systems serve as the nerve center, orchestrating the myriad functions and operations with precision and efficiency. Here, we’ll unravel the complexities of electronic control systems, empowering you to navigate and troubleshoot these digital domains with confidence and expertise.
A. Evolution of Electronic Control Systems
- Traditional Control Systems: In the past, appliances relied on mechanical or electromechanical controls, employing switches, relays, and timers to regulate operations. While effective, these systems lacked the flexibility and sophistication of their electronic counterparts.
- Transition to Electronic Controls: With advancements in microprocessor technology and digital electronics, appliances transitioned to electronic control systems in the late 20th century. These systems offer enhanced functionality, programmability, and diagnostic capabilities, revolutionizing the landscape of appliance design and repair.
B. Types of Electronic Control Systems
- Microcontroller-Based Systems: Many modern appliances feature microcontroller-based control systems, which utilize integrated circuits containing a microprocessor, memory, and input/output peripherals. These systems offer precise control over appliance functions and allow for software updates and customization.
- Programmable Logic Controllers (PLCs): In industrial and commercial appliances, PLCs are commonly employed to automate complex processes and sequences. These ruggedized controllers offer robust performance in harsh environments and can be programmed to perform a wide range of tasks.
C. Key Components and Functionality
- Microprocessors: At the heart of electronic control systems lie microprocessors, which serve as the central processing unit (CPU) responsible for executing instructions and managing operations. These silicon brains coordinate input/output signals, process sensor data, and execute control algorithms to regulate appliance functions.
- Memory: Electronic control systems utilize various types of memory, including Read-Only Memory (ROM) for storing firmware and instructions, Random-Access Memory (RAM) for temporary data storage, and Electrically Erasable Programmable Read-Only Memory (EEPROM) for storing user settings and configuration data.
- Input/Output Interfaces: Input/output interfaces facilitate communication between electronic control systems and external sensors, actuators, and user interfaces. These interfaces enable the monitoring of temperature, pressure, and other parameters, as well as the activation of motors, solenoids, and heating elements.
D. Real-World Application: Diagnosing a Faulty Oven Control Board
Imagine a scenario where a homeowner reports erratic behavior from their oven, with temperature fluctuations and display anomalies. Upon inspection, you discover a faulty oven control board, causing intermittent communication errors and control malfunctions. By replacing the defective control board and performing a system reset, you restore the oven to reliable and consistent operation, delighting the homeowner with a swift and effective repair.
Refrigeration System Diagnosis
In the realm of appliance repair, refrigeration systems are ubiquitous, powering a wide array of essential appliances such as refrigerators, freezers, and air conditioners. Understanding the intricacies of refrigeration system diagnosis is paramount for technicians, as these systems are prone to a variety of faults that can compromise their performance and efficiency. In this section, we’ll delve deep into the technical aspects of refrigeration system diagnosis, equipping you with the knowledge and skills needed to identify and rectify issues with precision and expertise.
A. Anatomy of a Refrigeration System
- Compressor: The compressor serves as the heart of the refrigeration system, compressing refrigerant gas and increasing its pressure and temperature. Understanding compressor operation and performance characteristics is essential for diagnosing issues such as inefficient cooling or compressor failure.
- Condenser Coil: The condenser coil dissipates heat from the refrigerant, causing it to condense into a liquid state. Issues with condenser coil cleanliness, airflow, or refrigerant flow can lead to overheating and reduced cooling capacity.
- Evaporator Coil: The evaporator coil absorbs heat from the refrigerated space, causing the refrigerant to evaporate and cool the surrounding air. Evaporator coil problems such as frost buildup, restricted airflow, or refrigerant leakage can result in insufficient cooling or frost-related issues.
- Expansion Device: The expansion device regulates the flow of refrigerant into the evaporator coil, controlling the refrigeration cycle. Issues with the expansion device, such as clogging or malfunction, can lead to improper refrigerant flow and temperature regulation.
B. Common Refrigeration System Faults
- Compressor Issues: Compressor failure, overheating, or inefficiency can result from electrical faults, mechanical wear, or refrigerant-related problems. Diagnosing compressor faults requires assessing electrical connections, measuring compressor performance, and analyzing refrigerant pressures.
- Refrigerant Leaks: Refrigerant leaks can occur due to corrosion, vibration, or mechanical damage to refrigeration system components. Detecting and repairing refrigerant leaks involves pressure testing, leak detection methods such as ultraviolet dye, and repairing or replacing damaged components.
- Evaporator and Condenser Coil Problems: Evaporator and condenser coil issues, such as dirt buildup, airflow restrictions, or coil damage, can impair heat transfer and reduce cooling efficiency. Cleaning coils, checking airflow, and inspecting for damage are essential steps in diagnosing and resolving coil-related faults.
- Expansion Device Malfunctions: Malfunctions in the expansion device, such as clogging, freezing, or improper adjustment, can disrupt the refrigeration cycle and lead to temperature fluctuations or system inefficiency. Testing expansion device operation and inspecting for blockages are key diagnostic steps in identifying and addressing these faults.
C. Diagnostic Techniques and Tools
- Pressure and Temperature Measurements: Utilizing pressure gauges and thermometers to measure refrigerant pressures and temperatures at various points in the refrigeration system provides valuable diagnostic information about system operation and performance.
- Refrigerant Leak Detection: Employing leak detection methods such as electronic leak detectors, ultraviolet dye, or nitrogen pressure testing to locate and repair refrigerant leaks ensures the integrity and efficiency of the refrigeration system.
- Electrical Testing: Conducting electrical tests on compressor motors, condenser fan motors, and other electrical components using multimeters or clamp meters helps identify faults such as motor winding failures, electrical shorts, or open circuits.
- Visual Inspection: Performing a visual inspection of refrigeration system components, including coils, piping, and connections, allows technicians to identify signs of damage, corrosion, or wear that may contribute to system faults.
D. Real-World Application: Resurrecting a Defunct Refrigerator
Imagine encountering a refrigerator that fails to cool properly, with frost buildup on the evaporator coil and audible compressor noises. Through a systematic diagnostic approach involving pressure testing, coil inspection, and compressor performance analysis, you identify a refrigerant leak and compressor inefficiency as the root causes of the issue. By repairing the refrigerant leak, replacing the compressor, and performing system evacuation and recharge, you restore the refrigerator to optimal cooling performance, delighting the customer with a successful repair.
Motor and Drive System Troubleshooting
In the realm of appliance repair, the proper functioning of motors and drive systems is crucial for the optimal performance of various appliances, including washing machines, dryers, dishwashers, and more. Understanding the intricate workings of these systems and employing effective troubleshooting techniques is essential for diagnosing and resolving faults with precision and expertise. In this section, we’ll delve deep into motor and drive system troubleshooting, equipping you with the knowledge and skills needed to tackle complex issues head-on.
A. Understanding Motor and Drive System Components
- Types of Motors: Appliances utilize various types of motors, including induction motors, brushed and brushless DC motors, stepper motors, and synchronous motors, each with its own unique characteristics and applications. Understanding the principles of motor operation and control is essential for diagnosing motor-related issues effectively.
- Drive Systems: Drive systems, such as belts, pulleys, gears, and couplings, transmit mechanical power from the motor to various components within the appliance, such as agitators, drums, or pumps. Issues with drive system components, such as wear, misalignment, or slippage, can result in performance degradation or failure of the appliance.
B. Common Motor and Drive System Faults
- Motor Failures: Motor failures can occur due to various factors, including electrical faults, mechanical wear, overheating, or bearing failure. Symptoms of motor failure may include abnormal noise, excessive vibration, or failure to start. Diagnosing motor faults requires assessing electrical connections, measuring motor current and voltage, and inspecting mechanical components for signs of wear or damage.
- Drive System Issues: Drive system issues, such as belt wear, misalignment, or tension loss, can result in reduced performance, noise, or component failure. Inspecting drive system components for wear, adjusting tension or alignment, and replacing worn components are essential steps in resolving drive system-related faults.
C. Diagnostic Techniques and Tools
- Electrical Testing: Conducting electrical tests on motors, including insulation resistance tests, continuity checks, and voltage measurements, helps identify electrical faults such as winding failures, shorts, or open circuits.
- Mechanical Inspection: Performing a visual inspection of drive system components, including belts, pulleys, gears, and couplings, allows technicians to identify signs of wear, misalignment, or damage that may contribute to system faults.
- Load Testing: Applying a load to the motor and observing its performance under load conditions can help diagnose issues such as motor overheating, excessive current draw, or insufficient torque output.
- Vibration Analysis: Utilizing vibration analysis tools and techniques to monitor motor and drive system vibrations can help identify mechanical issues such as bearing wear, misalignment, or resonance that may affect performance and reliability.
D. Real-World Application: Reviving a Silent Washing Machine
Imagine encountering a washing machine that fails to start, with no response from the motor when the cycle is initiated. Through a systematic diagnostic approach involving electrical testing, mechanical inspection, and load testing, you identify a faulty motor capacitor as the root cause of the issue.
Gas Appliance Diagnosis and Repair
Gas appliances play a crucial role in many households, providing efficient heating and cooking capabilities. However, due to the inherent risks associated with gas appliances, including the potential for gas leaks and combustion hazards, proper diagnosis and repair are essential for ensuring safety and reliability. In this section, we’ll delve into the technical intricacies of gas appliance diagnosis and repair, equipping you with the knowledge and skills needed to address gas-related issues with confidence and expertise.
A. Anatomy of Gas Appliances
- Key Components: Gas appliances, such as stoves, ovens, water heaters, and furnaces, consist of several key components, including gas valves, burners, igniters, thermocouples, and regulators. Understanding the function and operation of these components is essential for diagnosing and repairing gas appliance faults.
- Safety Features: Gas appliances are equipped with various safety features, including flame sensors, pressure regulators, and automatic shutoff valves, designed to detect and prevent potentially hazardous conditions, such as gas leaks or flame failures. Familiarizing yourself with these safety features is critical for ensuring the safe operation of gas appliances.
B. Common Gas Appliance Faults
- Ignition Failures: Ignition failures are a common issue with gas appliances and can occur due to a variety of factors, including faulty igniters, gas valve malfunctions, or thermocouple failures. Diagnosing ignition failures requires testing ignition components, checking gas supply pressure, and verifying electrical connections.
- Gas Leaks: Gas leaks pose a significant safety risk and can occur due to damaged gas lines, loose fittings, or faulty valves. Detecting and repairing gas leaks involves conducting a thorough visual inspection of gas lines and fittings, performing gas pressure tests, and utilizing gas leak detection tools, such as gas detectors or soapy water solutions.
- Incomplete Combustion: Incomplete combustion can result in the production of carbon monoxide, a deadly gas that poses a serious health risk. Identifying and addressing factors contributing to incomplete combustion, such as insufficient air supply, burner misalignment, or burner contamination, is essential for ensuring safe and efficient operation of gas appliances.
C. Diagnostic Techniques and Tools
- Gas Leak Detection: Utilizing gas leak detection tools, such as electronic gas detectors or combustible gas indicators, to identify and localize gas leaks in gas lines, fittings, or appliance components.
- Flame Analysis: Observing the characteristics of the flame, including color, shape, and stability, can provide valuable diagnostic information about combustion efficiency and burner performance.
- Gas Pressure Testing: Conducting gas pressure tests to verify proper gas supply pressure and identify potential issues with gas regulators, valves, or supply lines.
- Combustion Analysis: Performing combustion analysis tests to assess combustion efficiency, flue gas composition, and the presence of carbon monoxide using combustion analyzers.
D. Real-World Application: Restoring a Faulty Gas Range
Imagine encountering a gas range with inconsistent flame patterns and occasional ignition failures. Through systematic diagnostic testing, including gas pressure testing, flame analysis, and combustion analysis, you identify a partially clogged burner orifice and inadequate gas supply pressure as the root causes of the issue. By cleaning the burner orifice, adjusting gas pressure, and verifying proper combustion, you restore the gas range to safe and efficient operation, ensuring customer satisfaction and peace of mind.
The Importance of ARS Appliances Repair Service
In today’s fast-paced world, where households rely heavily on a multitude of appliances for daily tasks, the need for reliable and efficient appliance repair services cannot be overstated. ARS Appliances Repair Service stands as a beacon of expertise and reliability in the realm of appliance repair, offering unparalleled solutions to address the diverse needs of homeowners and businesses alike. Here, we’ll explore the significance of ARS Appliances Repair Service and why our expertise is indispensable in the world of appliance repair.
A. Expertise and Experience
ARS Appliances Repair Service boasts a team of highly skilled technicians with extensive experience and expertise in diagnosing and repairing a wide range of appliance faults. Our technicians undergo rigorous training and certification programs to stay abreast of the latest advancements in appliance technology, ensuring that they are well-equipped to tackle even the most complex repair challenges with confidence and precision.
B. Prompt and Reliable Service
At ARS Appliances Repair Service, we understand the inconvenience and frustration that can arise from appliance breakdowns. That’s why we prioritize prompt and reliable service, striving to address customer needs swiftly and effectively. With our fleet of service vehicles stocked with a comprehensive inventory of replacement parts and tools, we can respond to service calls promptly and complete repairs efficiently, minimizing downtime and disruption for our customers.
C. Commitment to Customer Satisfaction
Customer satisfaction lies at the core of everything we do at ARS Appliances Repair Service. From the moment a customer reaches out to us for assistance to the completion of the repair service, we prioritize open communication, transparency, and professionalism. Our goal is not only to resolve appliance issues but also to ensure that our customers feel valued, respected, and confident in the quality of our workmanship.
D. Comprehensive Repair Solutions
Whether it’s a malfunctioning refrigerator, a faulty oven, or a malfunctioning washing machine, ARS Appliances Repair Service offers comprehensive repair solutions to address a diverse range of appliance issues. From diagnosing the root cause of the problem to sourcing and installing replacement parts, our technicians are adept at delivering reliable and long-lasting repair solutions that restore appliances to optimal functionality.
E. Safety and Compliance
Safety is paramount in appliance repair, particularly when dealing with gas appliances or electrical systems. ARS Appliances Repair Service adheres to stringent safety protocols and industry best practices to ensure the safety of our technicians, customers, and their properties. Our technicians are well-versed in safety procedures and regulations governing appliance repair, minimizing the risk of accidents or injuries during the repair process.
F. Peace of Mind
By choosing ARS Appliances Repair Service, customers can enjoy peace of mind knowing that their appliance repair needs are in capable hands. Our commitment to excellence, reliability, and customer satisfaction sets us apart as a trusted partner in appliance repair, providing customers with the assurance that their appliances will be restored to optimal performance quickly, efficiently, and affordably.
Partnering with ARS for Reliable Appliance Repair
In the ever-evolving landscape of appliance repair, ARS Appliances Repair Service stands as a beacon of excellence, offering unmatched expertise, reliability, and customer satisfaction. As we’ve explored in this guide, the intricate workings of modern appliances demand the skills and knowledge of seasoned professionals, and ARS is proud to rise to the occasion.
With a team of highly skilled technicians, a commitment to prompt and reliable service, and a dedication to customer satisfaction, ARS Appliances Repair Service is more than just a repair service provider – we’re a trusted partner in keeping households and businesses running smoothly. From diagnosing complex issues to delivering comprehensive repair solutions, we take pride in our ability to restore appliances to optimal functionality, providing our customers with the peace of mind they deserve.
Whether it’s a malfunctioning refrigerator, a faulty oven, or a gas appliance in need of repair, customers can trust ARS to deliver prompt, reliable, and professional service every time. Our unwavering commitment to excellence and safety ensures that customers receive the highest quality repair services, backed by our expertise and experience in the field.
Thank you for considering ARS Appliances Repair Service for your appliance repair needs. We look forward to the opportunity to serve you and exceed your expectations with our unparalleled service and dedication to excellence.
For prompt and reliable appliance repair solutions, contact ARS Appliances Repair Service today.